Chevrolet Cruze Repair Manual: Installation Procedure
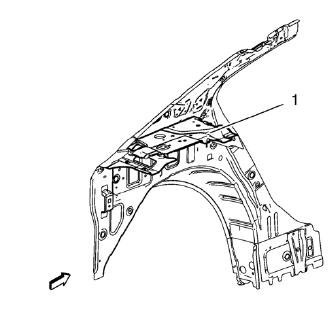
- Remove rear end upper panel extension (1) from service part.
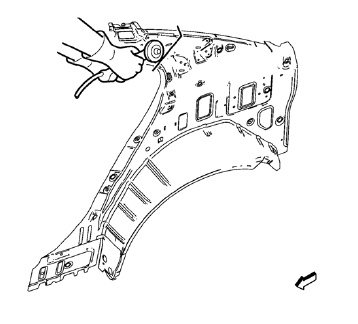
- Cut the body side inner panel in corresponding locations to fit the
remaining original panel. The sectioning joint should be trimmed to
allow a gap of one-and-one-half-times the metal thickness at the sectioning
joint.
- Create a 50 mm (2 in) backing plate from the unused portion of the
service part.
- Create 5 x 18 mm (4/16 x 11/16 in) slots for MIG-brazing along the
sectioning cut on the remaining original part. Locate these holes
13 mm (1/2 in) from the edge of part and spaced 40 mm (1 1/2 in) apart.
- Prepare all mating surfaces as necessary.
- Fit the backing plates halfway into the sectioning joints, clamp in
place and plug weld to the vehicle.
- Align the body side inner panel.
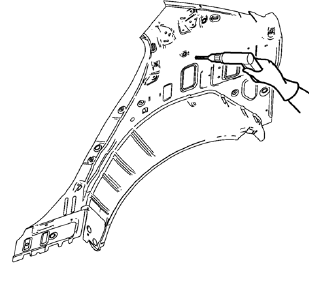
- Create 6 x 20 mm (4/16 x 12/16 in) slots for MIG-brazing in locations
where you can not apply a resistance spot
welder.
- Clean and prepare the attaching surfaces for spot welding and brazing.
Note: In MIG-brazing areas 50 mm (2 in) must be kept clear of
structural adhesive.
- Apply structural adhesive to all attaching surfaces
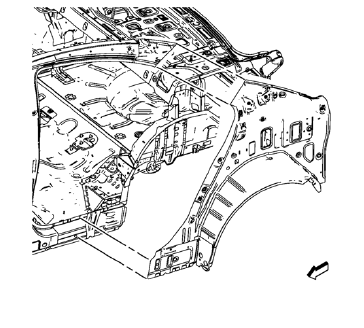
- Position the body side inner panel.
- Verify the fit of the panel.
- Clamp the body side inner panel into position.
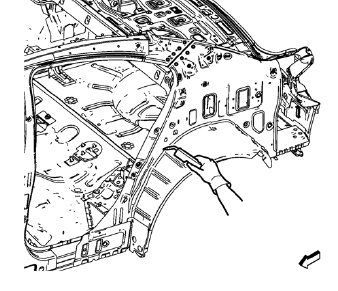
- Braze accordingly.
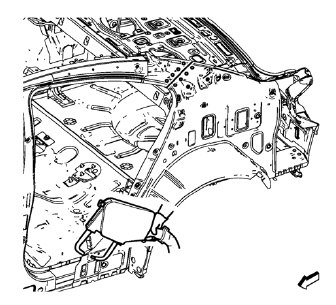
- Spot weld accordingly
- To create a solid braze with minimum heat distortion, make 25 mm (1 in)
stitch brazes along the seam with 25 mm (1 in) gaps
between them. Then go back and complete the stitch braze.
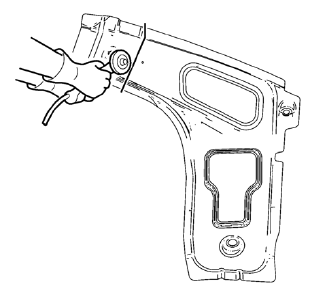
- Cut the body lock pillar upper reinforcement in corresponding locations
to fit the remaining original panel. The sectioning joint should
be trimmed to allow a gap of one-and-one-half-times the metal thickness at
the sectioning joint.
- Create a 50 mm (2 in) backing plate from the unused portion of the
service part.
- Create 5 x 18 mm (4/16 x 11/16 in) slots for MIG-brazing along the
sectioning cut on the remaining original part. Locate these holes
13 mm (1/2 in) from the edge of part and spaced 40 mm (1 1/2 in) apart.
- Prepare all mating surfaces as necessary.
- Fit the backing plates halfway into the sectioning joints, clamp in
place and braze to the vehicle.
- Align the body lock pillar upper reinforcement.
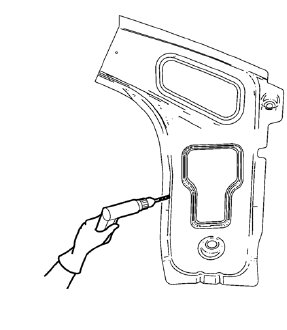
- Create 6 x 20 mm (4/16 x 12/16 in) slots for MIG-brazing in locations
where you can not apply a resistance spot welder.
- Clean and prepare the attaching surfaces for spot welding and brazing.
Note: In MIG-brazing areas 50 mm (2 in) must be kept clear of
structural adhesive.
- Apply structural adhesive to all attaching surfaces
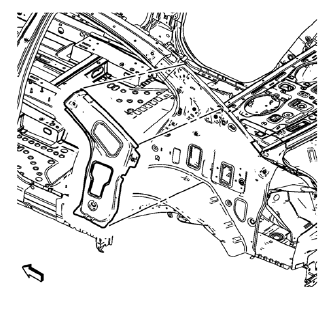
- Position the body lock pillar upper reinforcement.
- Verify the fit of the panel.
- Clamp the body lock pillar upper reinforcement into position.
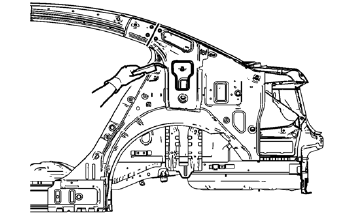
- Braze accordingly.
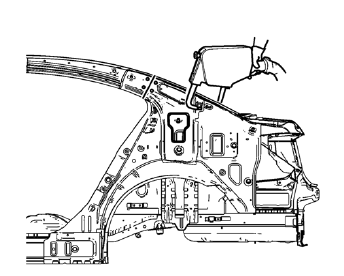
- Spot weld accordingly.
- Apply the sealers and anti-corrosion materials to the repair area, as
necessary. Refer to Anti-Corrosion Treatment and Repair.
- Paint the repaired area. Refer to Basecoat/Clearcoat Paint Systems.
- Install all related panels and components.
- Connect the negative battery cable. Refer to Battery Negative Cable
Disconnection and Connection.
- Enable the SIR system. Refer to SIR Disabling and Enabling.
Warning: Refer to Approved Equipment for Collision Repair Warning in the
Preface section.
Warning: Refer to Collision Sectioning Warning in the Preface section.
Warning: Refer to Glass and She ...
Note: According to different corrosion warranties, only the
regional mandatory joining methods are allowed. ...
Other materials:
Power Steering
Specifications
Power Steering System Bleeding
Note:
Use clean, new power steering fluid type only. See the Maintenance
and Lubrication subsection for fluid specifications.
Hoses touching the frame, body or engine may cause system noise.
Verify that the hoses do not touch any ot ...
Engine Overheating
There is an engine coolant temperature gauge on the vehicle instrument cluster
to warn of engine overheating.
If the decision is made not to lift the hood when this warning appears, get service
help right away.
If the decision is made to lift the hood, make sure the vehicle is parked on
a le ...
Vehicle Load Limits
It is very important to know how much weight the vehicle can carry. This weight
is called the vehicle capacity weight and includes the weight of all occupants,
cargo, and all nonfactory-installed options.
Two labels on the vehicle show how much weight it may properly carry: the Tire
and Loadi ...